Revolutionizing Product Development with Injection Molded Prototypes
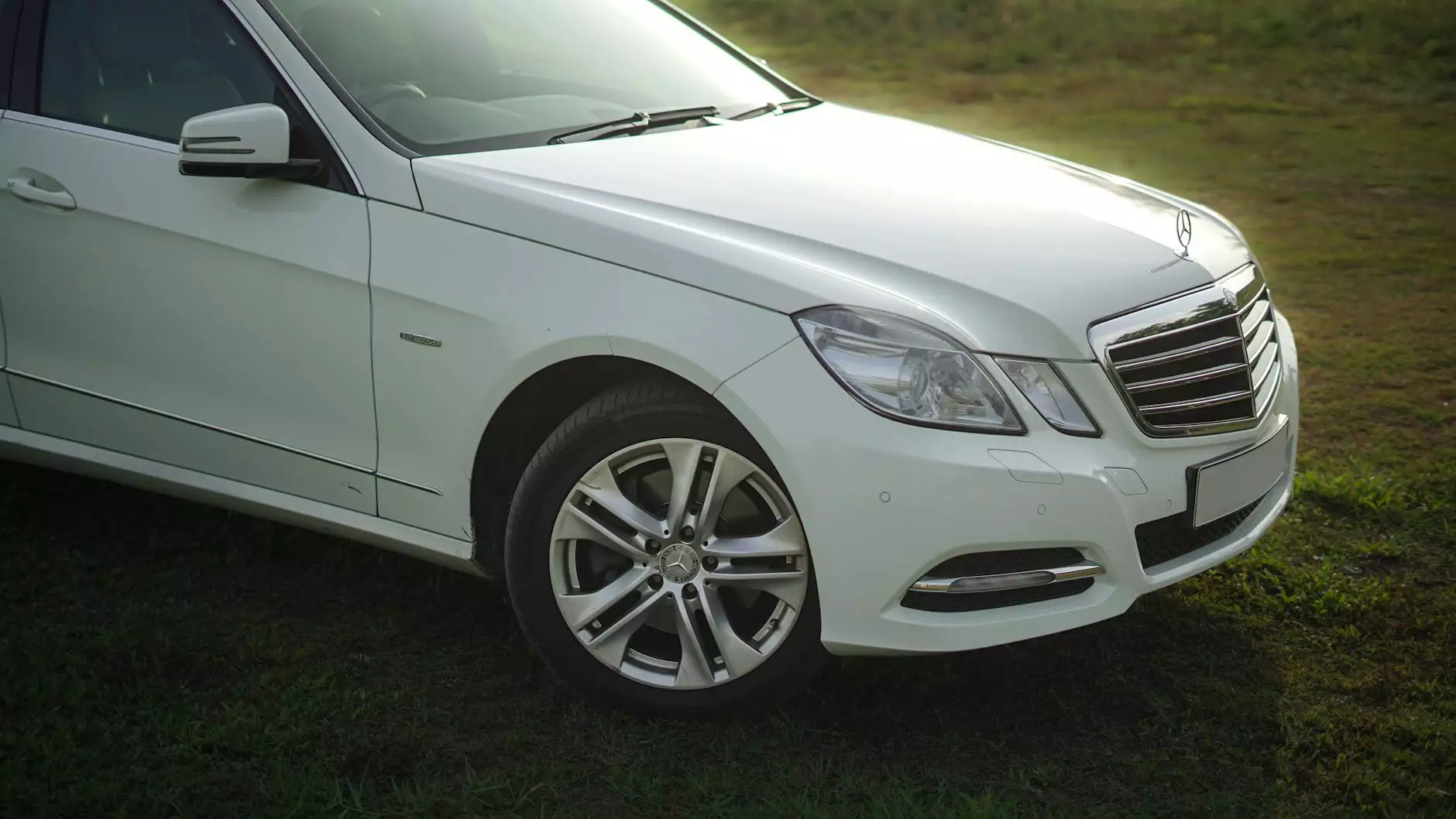
Injection Molded Prototypes have become a game changer in the field of manufacturing and product development. At DeepMould.net, we specialize in delivering high-quality metal fabrications that push the boundaries of innovation. This article delves deep into the advantages of injection molded prototypes, their applications, and how they enhance the efficiency of product development processes.
What Are Injection Molded Prototypes?
Injection molded prototypes are preliminary models created using advanced injection molding technology. This process involves injecting molten material (usually plastic) into a mold to produce parts that closely resemble the final product. These prototypes are crucial for:
- Testing designs and functionality
- Validating ideas before mass production
- Identifying potential improvements
The Process of Injection Molding
The injection molding process consists of several key steps, ensuring precision and consistency. Here’s a breakdown of the process:
- Design and Development: Collaborating with designers, we create CAD models that depict the product’s dimensions and specifications.
- Mold Creation: High-quality molds are manufactured, usually from steel or aluminum, which will form the basis of the prototype.
- Injection Phase: The selected plastic material is heated until it melts and is then injected into the mold under high pressure.
- Cooling and Ejection: The molten plastic cools and solidifies within the mold, after which the finished prototype is ejected.
- Finishing Touches: Prototypes often undergo finishing processes such as sanding, painting, or assembly to meet aesthetic and functional requirements.
Advantages of Using Injection Molded Prototypes
Utilizing injection molded prototypes offers several distinct advantages:
1. Cost-Effectiveness
Preventing costly mistakes is crucial. By developing prototypes first, companies can assess the functionality and design of a product before investing in mass production.
2. Speed to Market
In today’s competitive landscape, speed is essential. Injection molded prototypes allow rapid production, ensuring that businesses can introduce their products to market more quickly.
3. Design Flexibility
Prototyping enables iterative design processes, meaning adjustments can be made based on testing feedback without significant delays.
4. High Accuracy and Quality
Injection molding offers precise control over dimensions, resulting in prototypes that are closely aligned with the final product specifications.
5. Variety of Materials
Injection molding accommodates a range of materials, including various plastics and composites, allowing businesses to choose the right material for their prototypes.
Applications of Injection Molded Prototypes
The versatility of injection molded prototypes is evident across numerous industries. Some notable applications include:
1. Automotive Industry
In the automotive sector, prototypes are essential for testing components such as dashboards, trims, and other plastic parts, ensuring they meet safety and aesthetic standards.
2. Consumer Electronics
From smartphone casings to electronic housings, prototypes developed through injection molding allow for rigorous testing of design and usability in a competitive market.
3. Medical Devices
The medical field demands precision; hence, injection molded prototypes help ensure that devices meet stringent regulatory standards for functionality and safety.
4. Household Products
From kitchenware to furniture fittings, prototypes allow companies to innovate and test new product concepts effectively.