The Power of Mold Injection Plastic in Modern Manufacturing
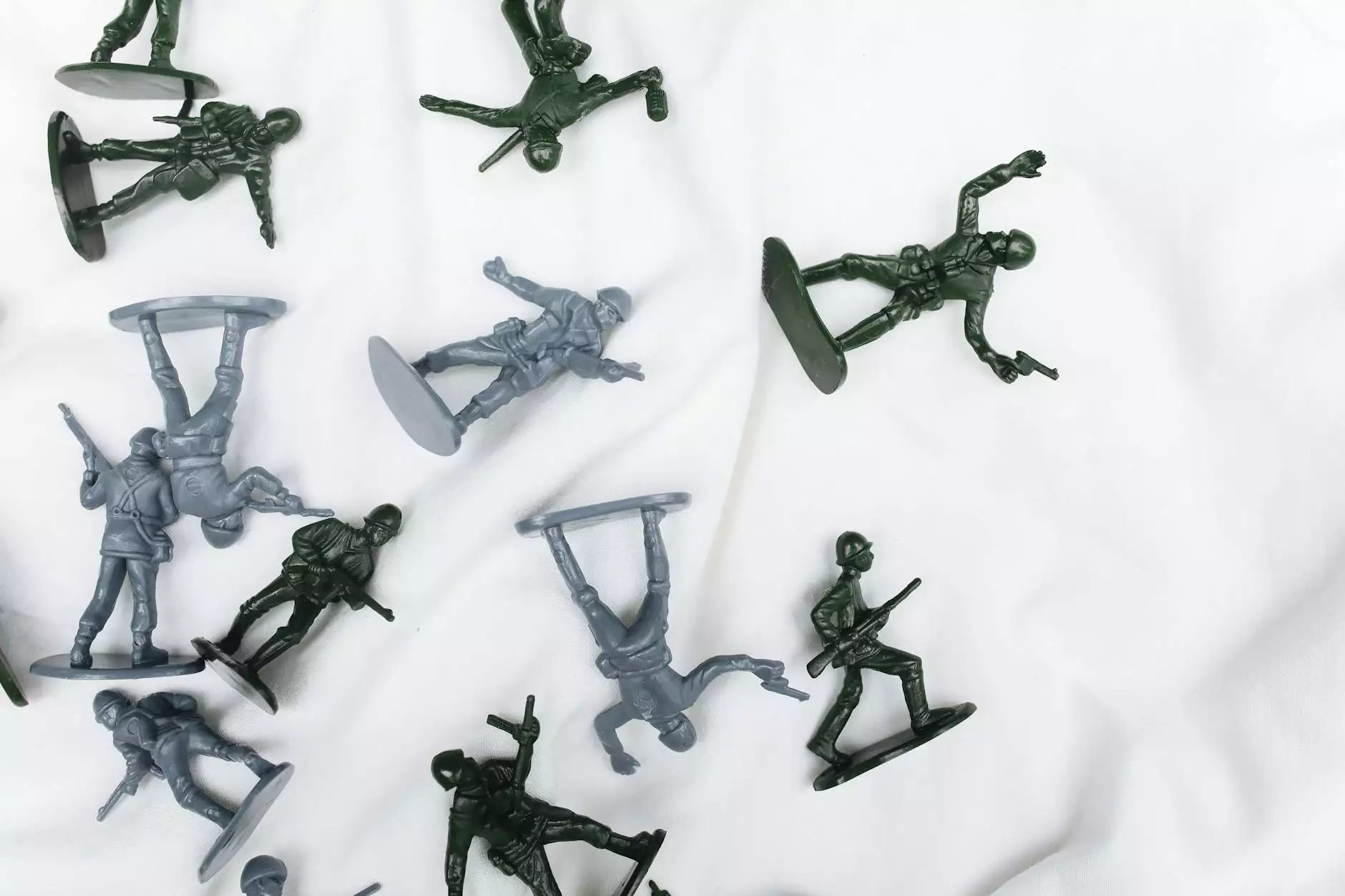
In today's fast-paced industrial landscape, the need for efficient, durable, and cost-effective manufacturing processes has never been more critical. One of the standout techniques that has revolutionized production is mold injection plastic. This innovative method allows for the rapid production of complex plastic parts with unparalleled precision and consistency.
Understanding Mold Injection Plastic
Mold injection plastic is a manufacturing process that involves injecting molten plastic into a pre-designed mold to form desired shapes and sizes once cooled. This technique is favored for its ability to produce large volumes of identical parts quickly and with minimal waste, making it ideal for various applications across numerous industries.
Advantages of Mold Injection Plastic
The use of mold injection plastic offers numerous benefits that contribute to its widespread popularity:
- Cost-Effectiveness: Once the initial mold is created, the cost per part significantly decreases, making it economically viable for large-scale production.
- Design Flexibility: Designers can create complex geometries that would be difficult or impossible to achieve with other manufacturing methods.
- Consistency and Quality: With high precision machinery and controlled processes, each part produced is consistent in quality and specification.
- Reduced Waste: The process minimizes material waste compared to traditional machining or cutting techniques.
- Speed: Rapid production cycles allow companies to meet tight deadlines and increase throughput.
Applications of Mold Injection Plastic
The applications of mold injection plastic are vast and varied, spanning multiple sectors including:
1. Automotive Industry
In the automotive sector, mold injection plastic is used to produce a wide array of components such as dashboards, interior trim, and housings for headlights and taillights. These components benefit from the lightweight nature of plastics, contributing to better fuel efficiency.
2. Consumer Electronics
Electronics manufacturers utilize mold injection to create intricate casings for devices like smartphones, tablets, and laptops, which require both durability and aesthetic appeal.
3. Medical Devices
The healthcare industry frequently relies on mold injection plastic for the production of medical devices and equipment. The ability to create sterile, precise, and lightweight components is vital in this field.
4. Household Goods
From kitchen utensils to storage solutions, the versatility of mold injection plastic allows manufacturers to produce a plethora of household items, catering to consumer needs and preferences.
5. Packaging
Innovative packaging solutions for food and consumer products are often developed using mold injection plastic, offering protection while maintaining visual appeal.